Below is some of my work from my 2 and a half year time at Arrgh Manufacturing Company. My work at Arrgh began with translating and documenting existing products into 2D and 3D CAD models. By my second year, I was in charge of designing an updated product line from scratch. This included a heavy emphasis on using "universal" parts across the various sizes, leading to an overall reduction in cost by up to 15%.
A standard 24" x 24" vent box that was the basis of my updated product line. This model uses 4 fans and an internal louver set
The louver control gearing to close the vent boxes. Gears were selected and fitted to use an existing motor design.
The complete louver assembly. In the foreground is the gearing with the drive motor being on the opposite side of the assembly.
A side project I worked on with my boss. This is a recreated oil pump for an older model BMW engine.
One of the injection molded plastic parts I translated into CAD. This was done by measuring multiple parts with precision calipers and using the average values across the different parts to account for manufacturing tolerances.
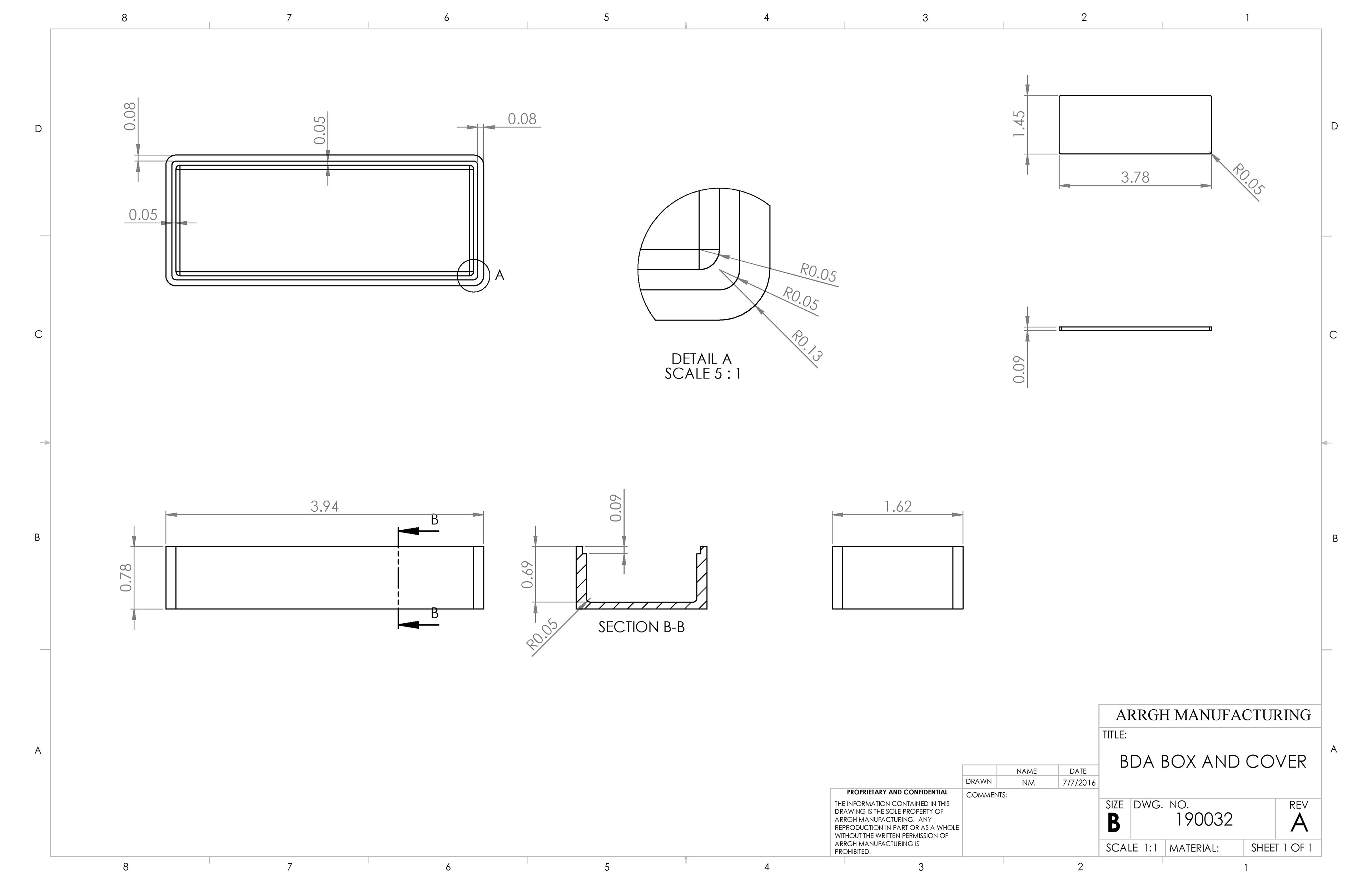
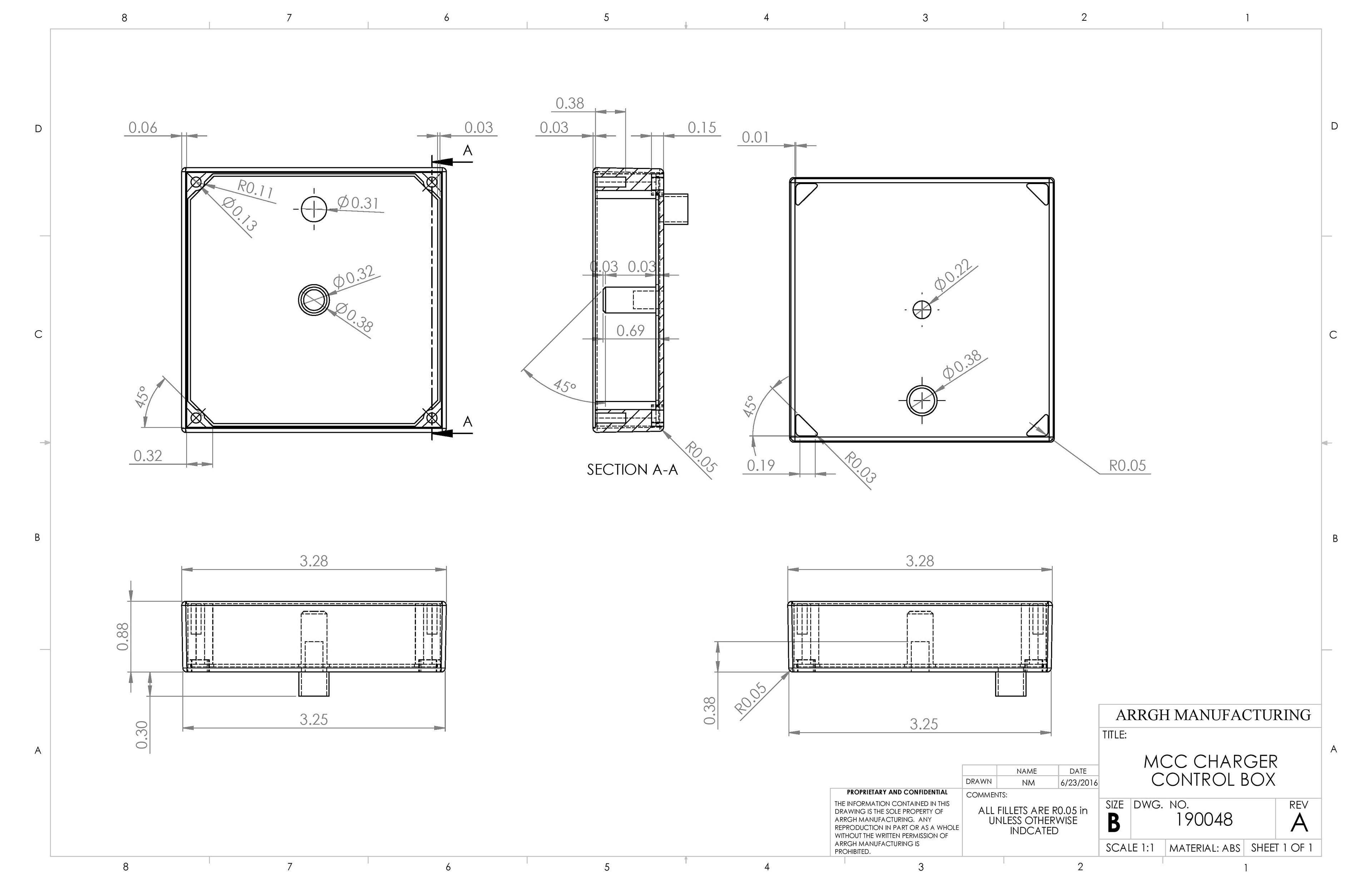
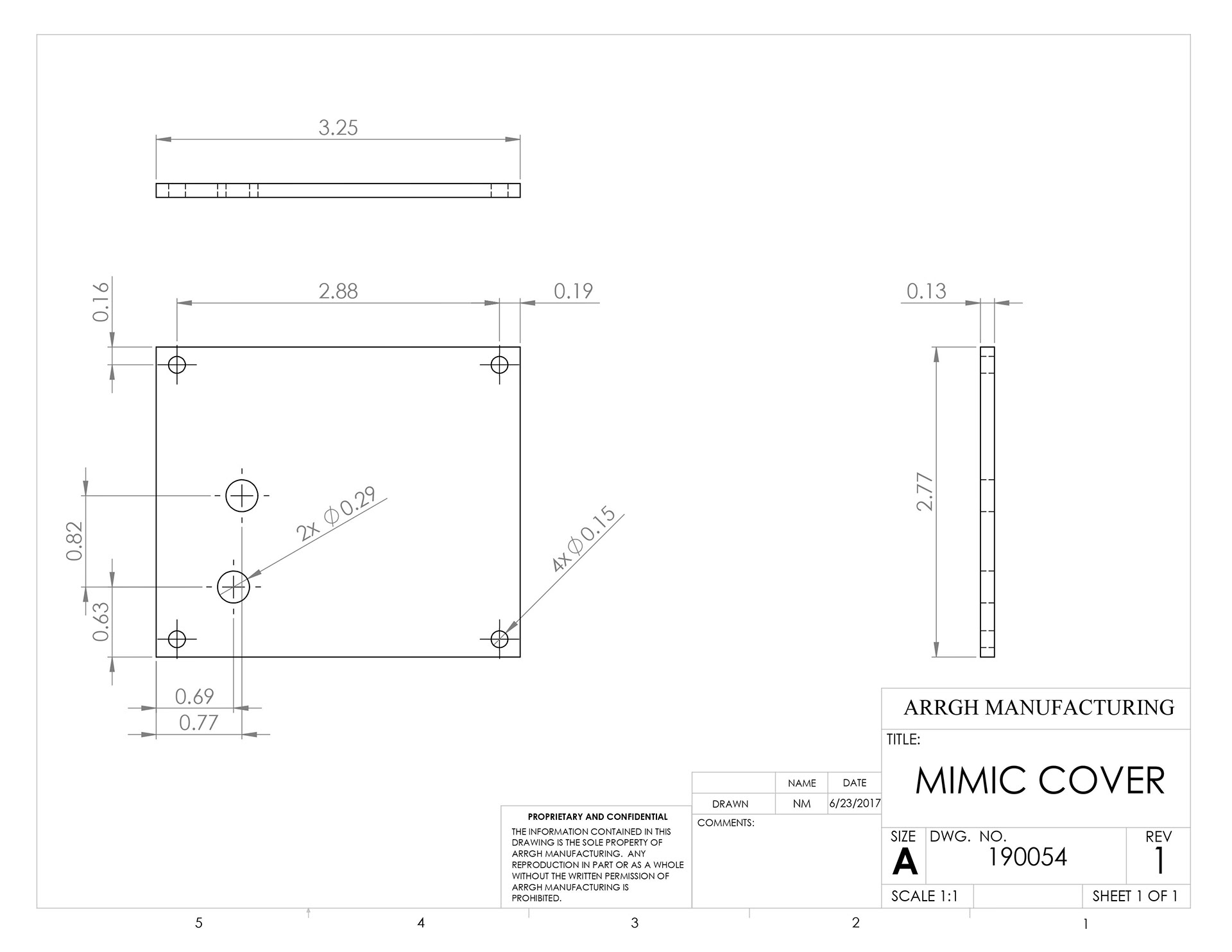
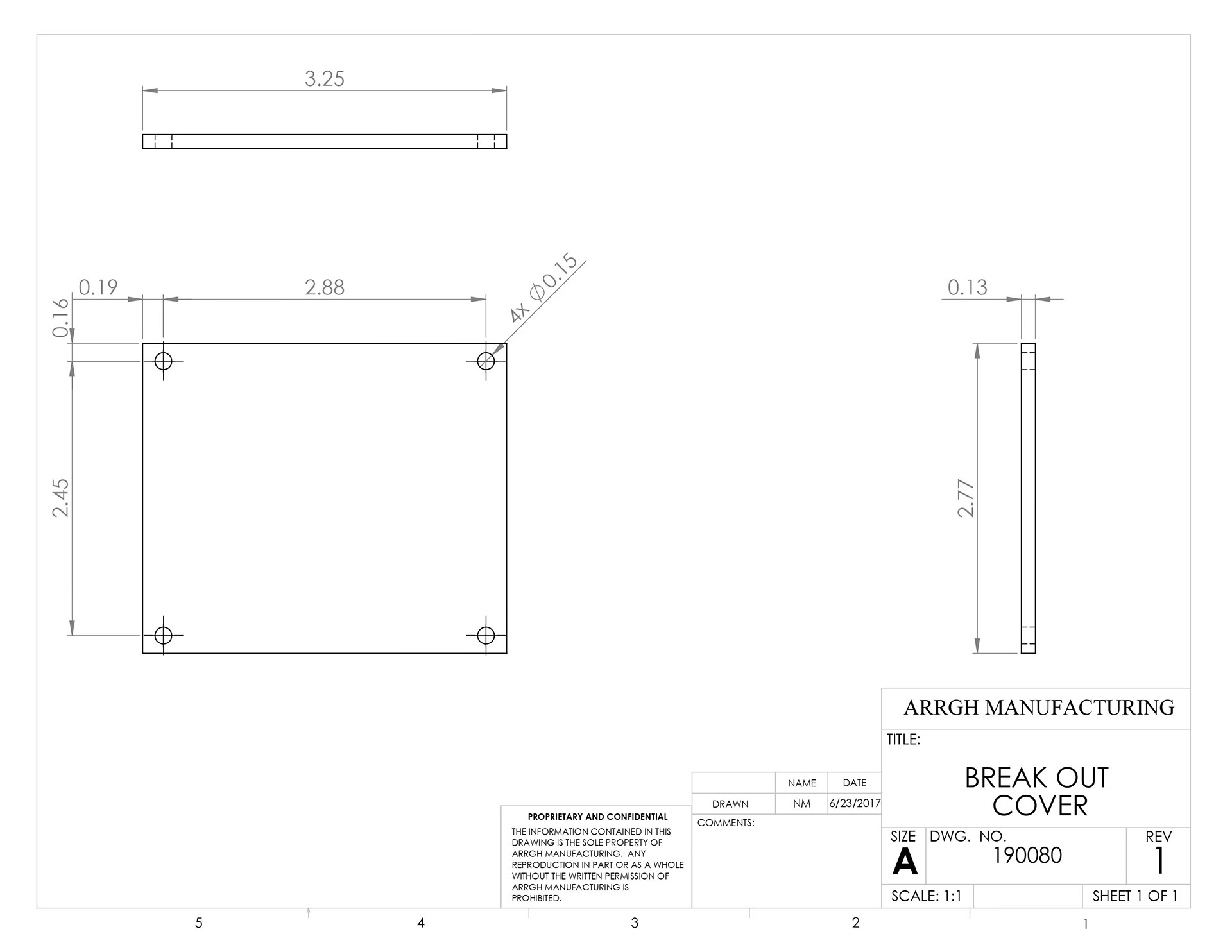
Simple injection molded parts I recreated in CAD. The draft on the parts was not identifiable at the time so I modelled each part in their basic, untoleranced and undrafted forms.