STEAM Create is a company I launched to combine my passions for design and 3D printing. My goal is to create unique products made accessible via additive manufacturing. The first of these is a Rising Iris Ring Box intended for engagement rings. Below is the development process for the first unit as well as a link to purchase the latest design.
Project Objective:
Create a 3D printed gift box that combines the following components which actuate in one motion:
-An opening Iris mechanism lid
-A rising platform
-Rotation at/near the base preferred
Final box should about 2.5 inches wide and 2.5 inches tall and be easily created with FDM/FFF printing.
Create a 3D printed gift box that combines the following components which actuate in one motion:
-An opening Iris mechanism lid
-A rising platform
-Rotation at/near the base preferred
Final box should about 2.5 inches wide and 2.5 inches tall and be easily created with FDM/FFF printing.
Problem Statements:
How do I link the iris opening with the platform rising in one (rotational) motion?
Additionally, developing the iris mechanism required significant trial and error along with multiple
adjustments to linkage lengths and shapes.
Finally, choosing to focus on the rising platform before the iris meant that major design parameters
needed to be updated even after being “locked”.
Additionally, developing the iris mechanism required significant trial and error along with multiple
adjustments to linkage lengths and shapes.
Finally, choosing to focus on the rising platform before the iris meant that major design parameters
needed to be updated even after being “locked”.
Initial Proof of Concepts for Rising Platform
Goals:
● Test and prove using a pin and helical slot
as method of raising platform
● Determine pin material (3D printed, OTS metal, etc)
Outcomes:
● Validated pin and helical slot method
● Confirmed 3DP material viable with slight modification
Goals:
● Test and prove using a pin and helical slot
as method of raising platform
● Determine pin material (3D printed, OTS metal, etc)
Outcomes:
● Validated pin and helical slot method
● Confirmed 3DP material viable with slight modification
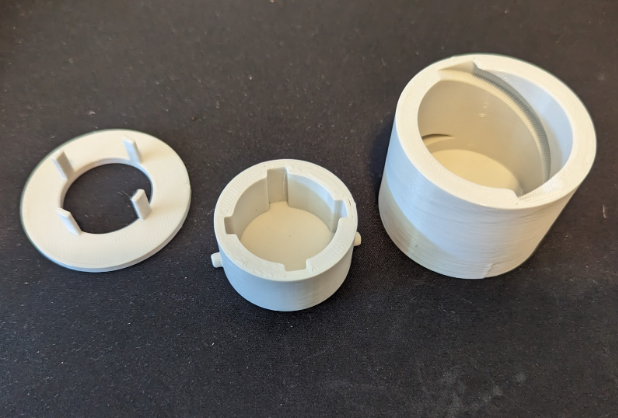
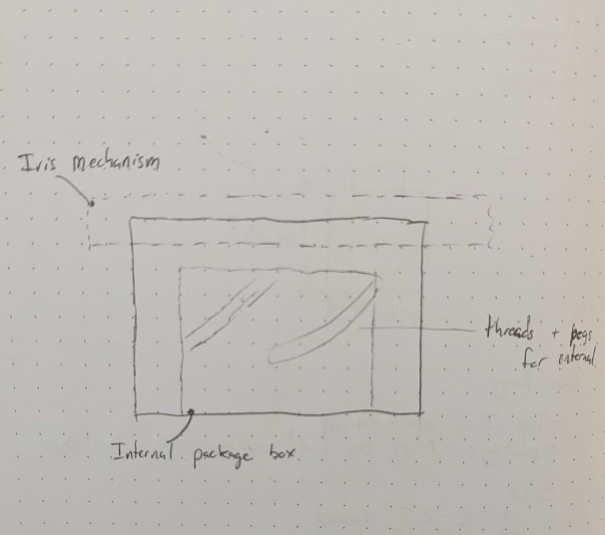
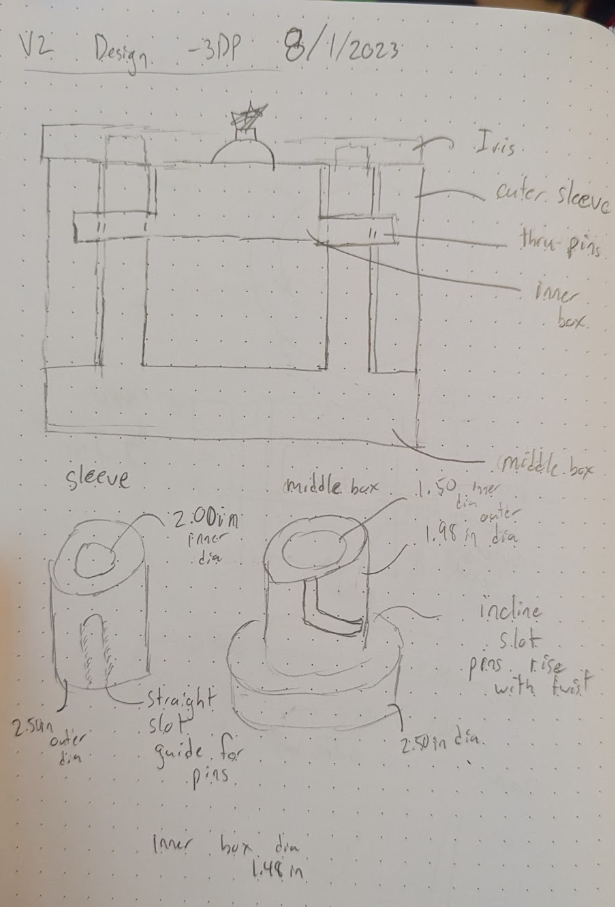
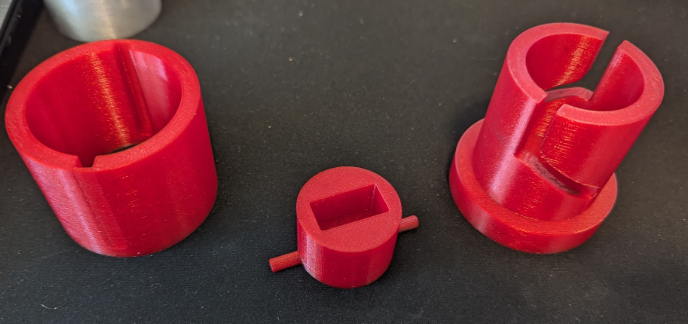
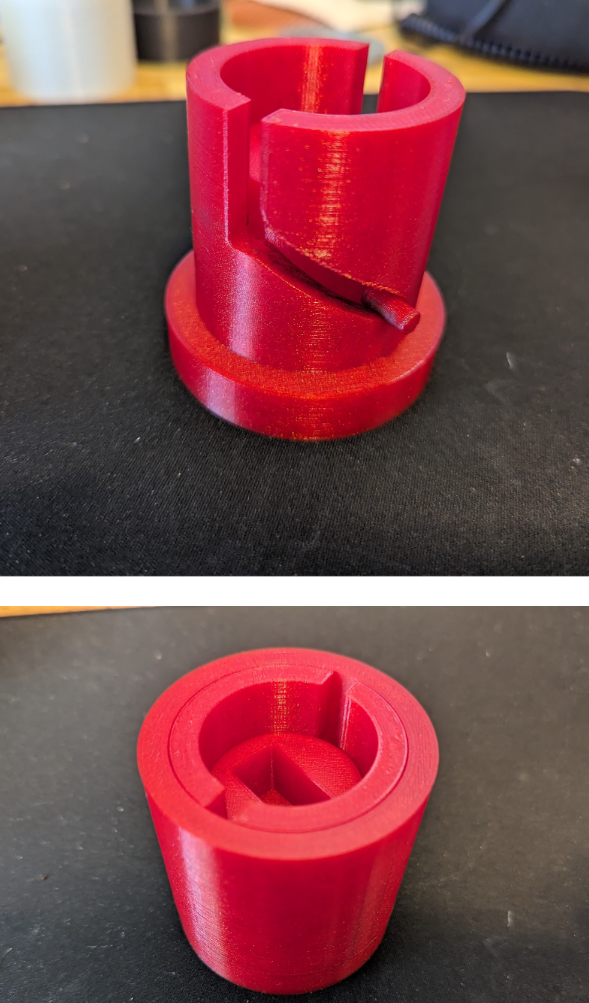
Refocus on design goals
Clean link between iris and platform rising
Box rotation preferred at/near base
Outcomes
Updated design to use 3 “layers”:
Inner platform with pins
Middle box with slots for pins to pass through
Outer sleeve to induce motion on pins
Initially spec’ed for ~45 degree turn
Narrowed down to 2 options to constrain iris leaves
Slotted Ring
Hidden beneath leaves
Less parts - can be integrated into outer sleeve
“Arm” Linkages
More compact in the closed state
Arms are shown in open state - more interesting visually
Significantly more parts for assembly and tolerance stackup
Outcome
Arm linkages chosen. Mostly for visual appeal.
Linkage arc lengths required testing (simulation and prototype) and a few iterations to dial in.
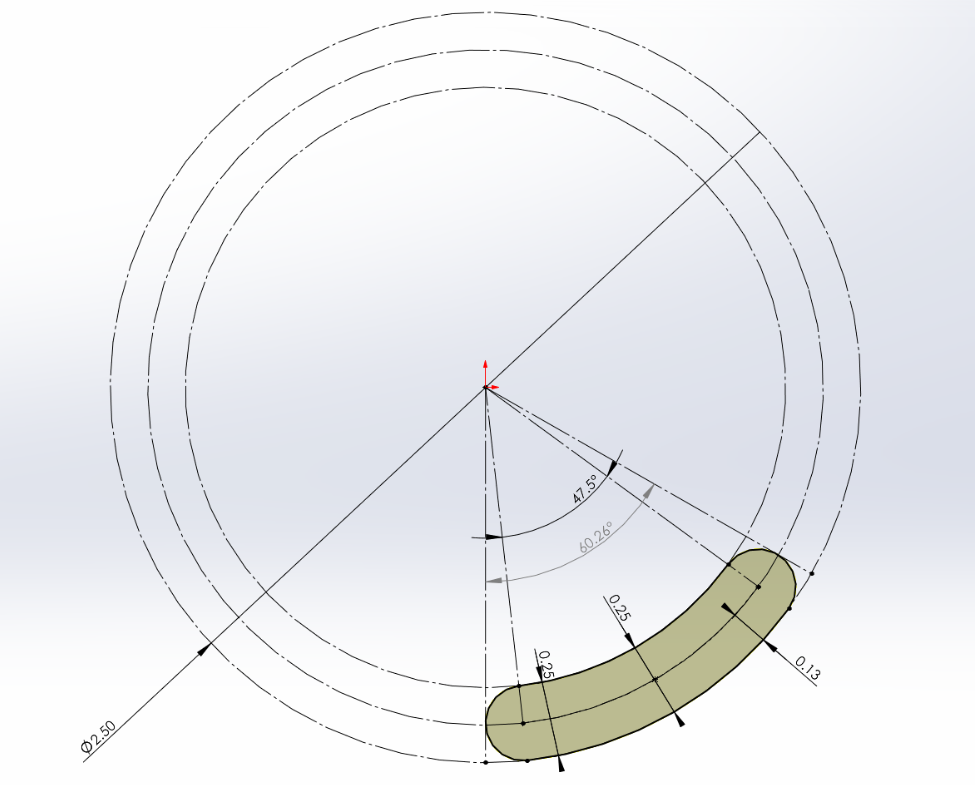
Analyzing the couple motions in Solidworks
By correctly assigning mates to reflect the real-world assembly, Solidworks Motion Studies can be used to find collisions and refine the design
Design changes
Added holes to the middle box and outer sleeve to install iris leaves and arms
Updated helical slot slope to pair with rotation limit imposed by iris (~32 degrees)
Decreased overall height
Downsized hardware from M3 to M2
Reduced clearances to remove slop and rattle in assembly
Outer sleeve ID to middle box OD
Platform pins to middle box helical slot
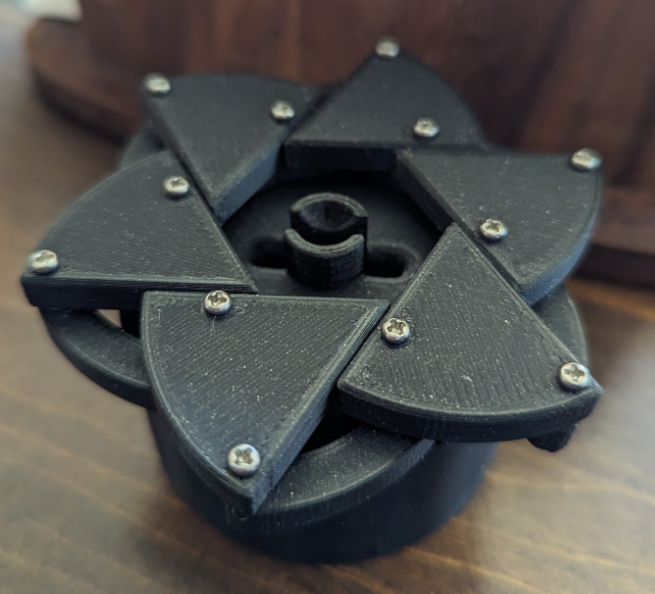
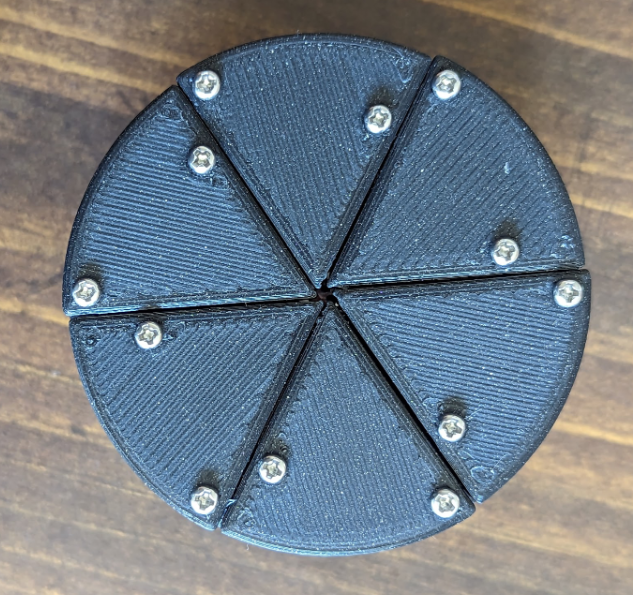
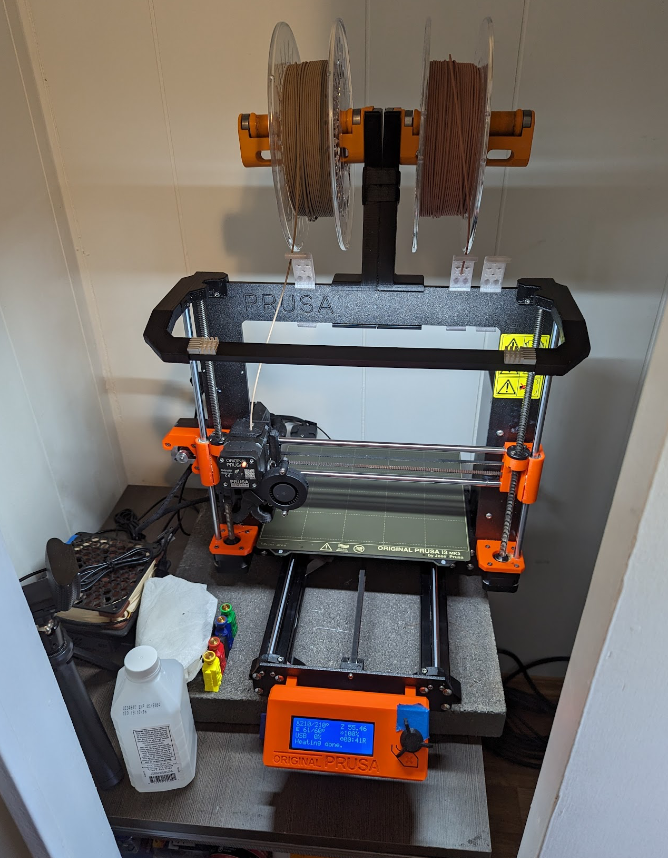
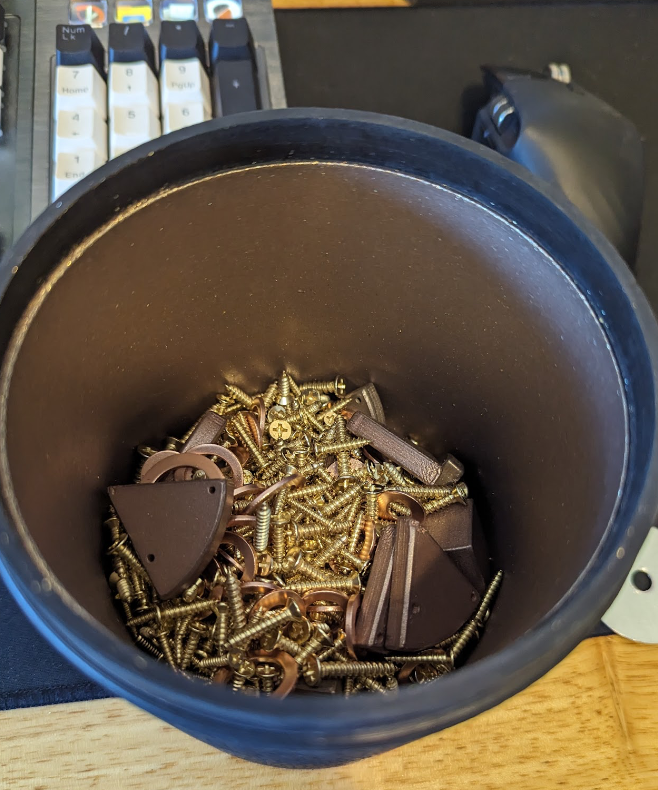
Material changes vs prototypes
Prototypes printed in various basic PLA
Final Assembly printed with Colorfabb metal-fill PLA (Stainless Steel, “Bronze” and Copper)
All parts printed on Prusa MK3S+ with a 0.6mm nozzle
Metal-fill parts processed in rock tumbler with brass screws and copper washers as media for 6-10 hours
This exposes the metal particles in the filament in addition to reducing layer lines
Parts cleaned and polished before final assembly
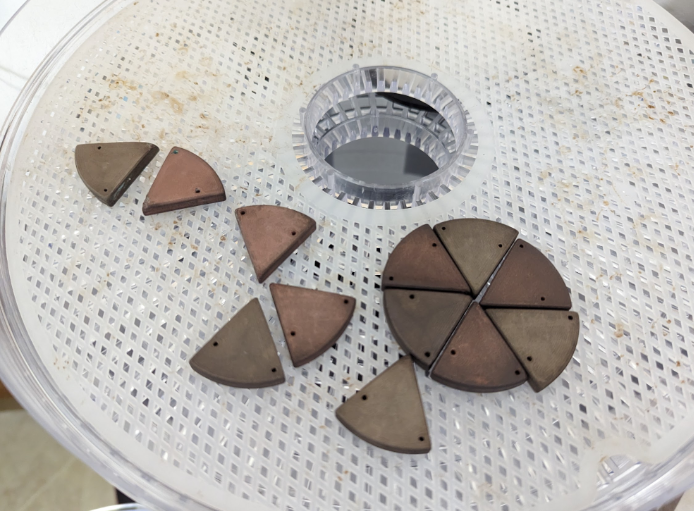
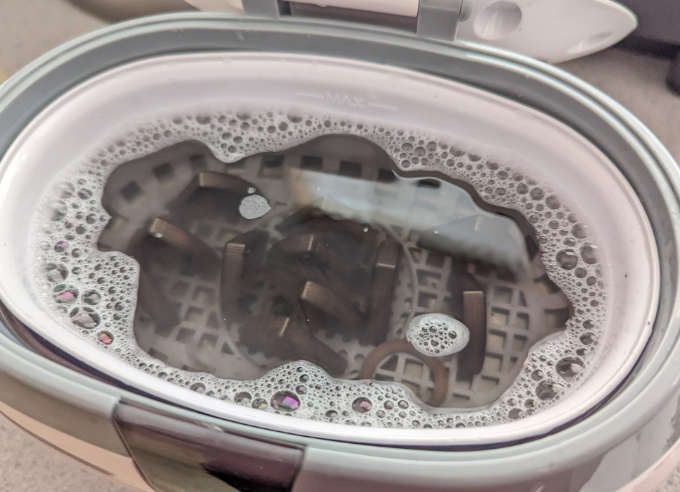
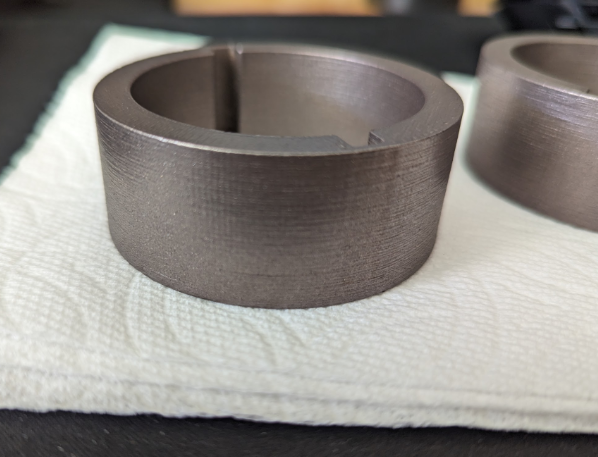
Final Assembly
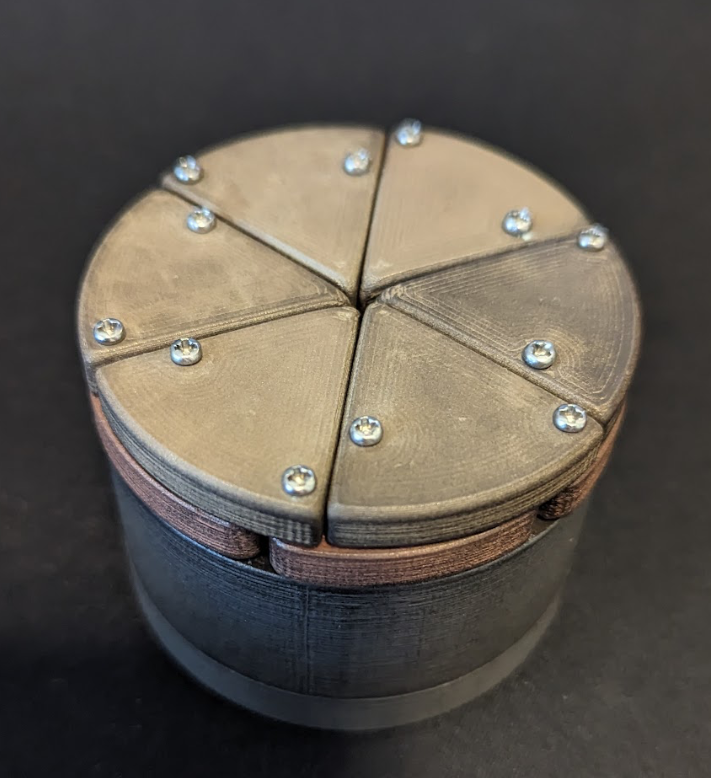
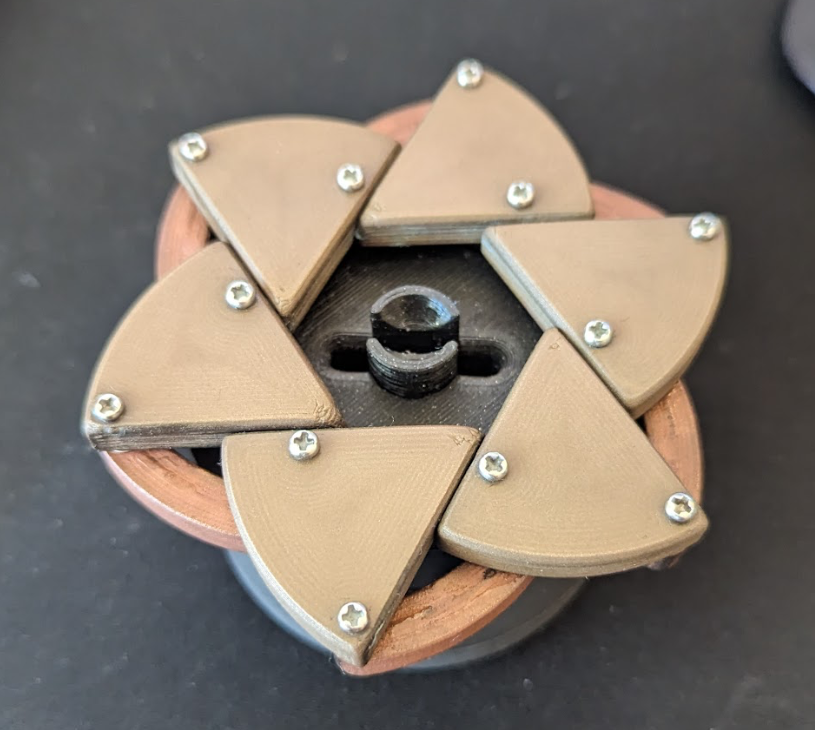
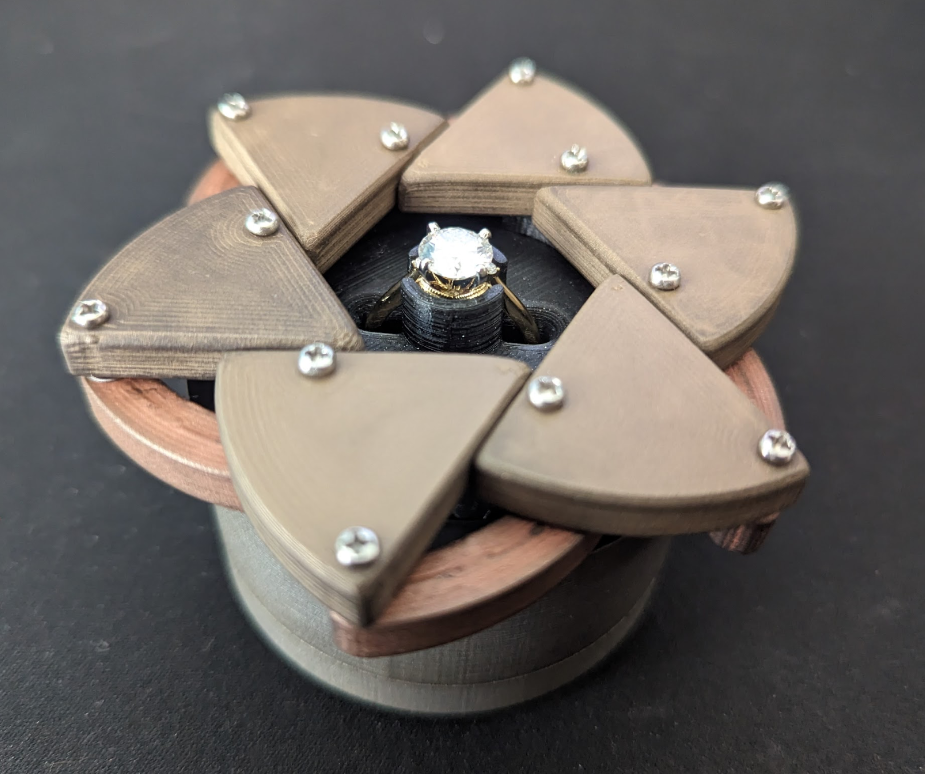